Basic Info.
Product Description
Fuel oil water separator centrifuge with filter system
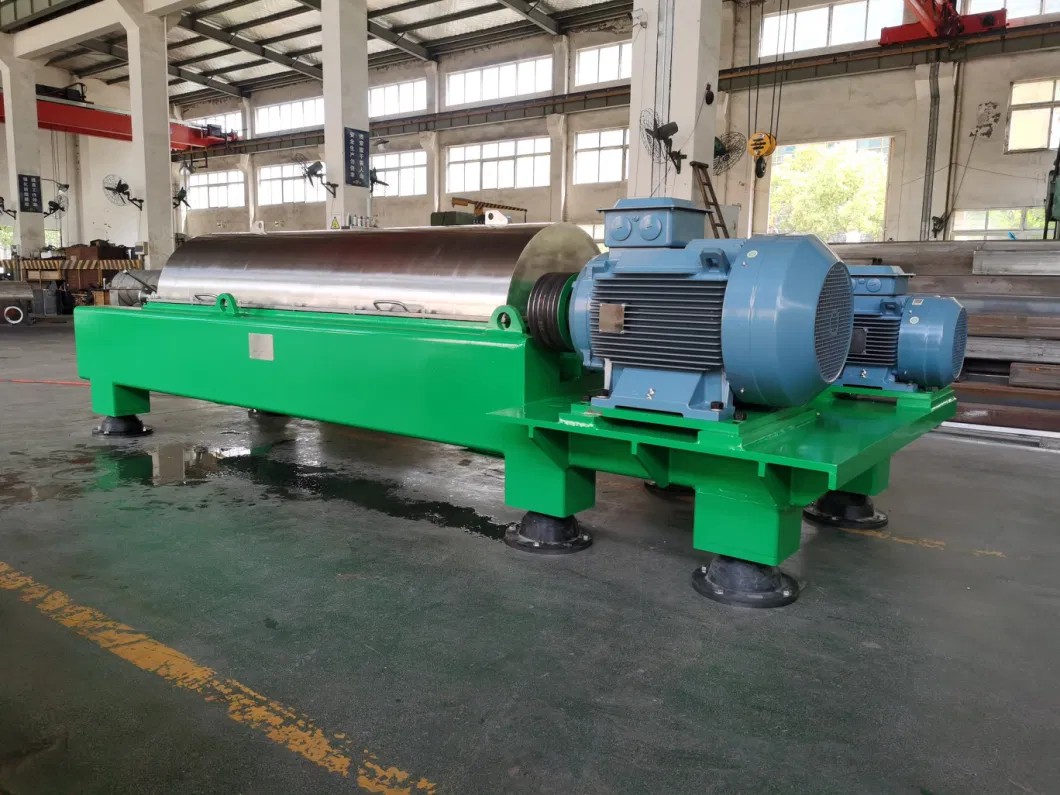
Decanter Centrifuge Features and Benefits:
1. Innovative design includes longer bowl, allowing drilling fluids to thread through more slowly, thus resulting in drier solids and finer separation point;
2. Big bowl offers big volume. It also generates high-G force;
3. Stainless steel bowl, scroll, compartment are available and covered with corrosion-proof coating so as to have longer lifespan;
4. Tungsten carbide scroll points with wide spacing flights at tapered end create a finer layer of conveyed solids for consistent, uniform separation and maximum solids control efficiency.
5. German FAG or Swedish SKF brand bearings are available;
6. Electrical Components complies with SIEMENS/Schneider ATEX or IEC Ex.
7. Screw pump and submersible slurry pump are provided to meet liquid feeding requirements of centrifuge of various customers
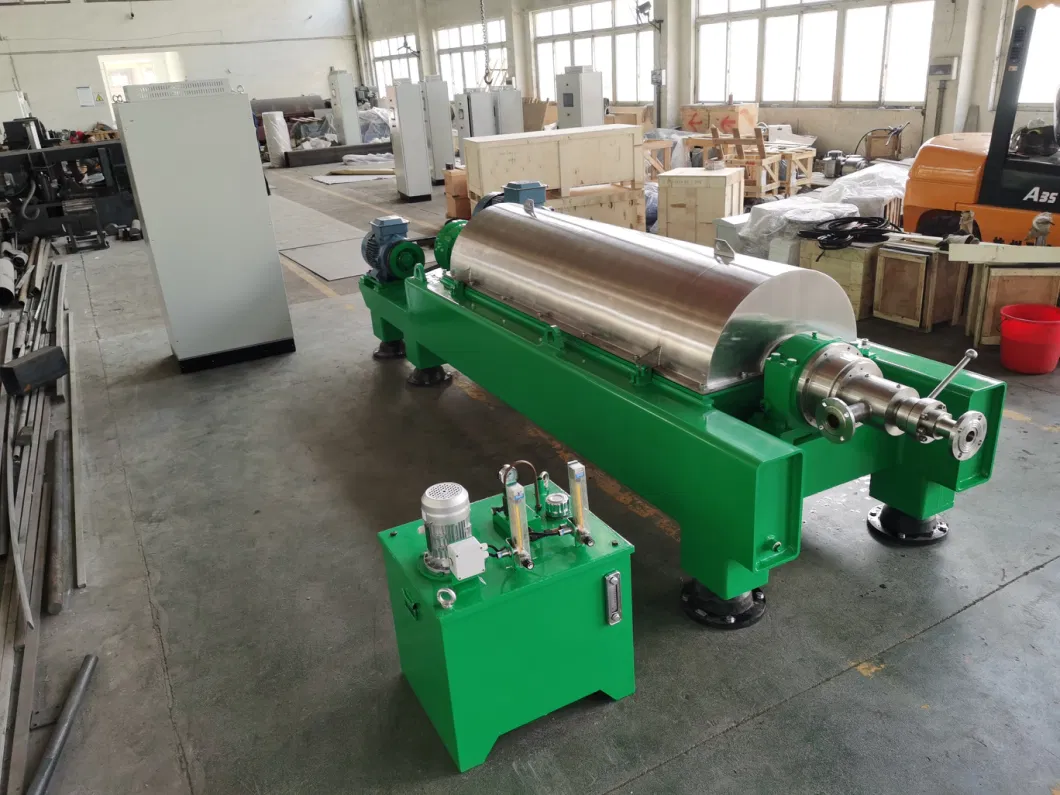
The separation process in a decanter centrifuge relies on a few process characteristics such as centrifugal force or G-force, sedimentation rate and separating factor, differential speed between the conveyor and bowl, and clarity of the liquid discharge.Decanter centrifuges require a centrifugal force for the separation of the solids from the liquid. This characteristic is dependent on the radius of the centrifuge and its angular rotational speed. A decanter centrifuge applies a force equivalent to several thousand G's, which reduces the settling time of the particles. It is also favored to maintain a large G-force, which will result in an improved separation.
The rate at which sedimentation occurs is an important characteristic of the decanter centrifuge separation process. The
sedimentation rate is influenced by the particle size, the shapes of the particles, their differential densities and the viscosity between the particles and the liquid. This process characteristic can be improved by utilizing flocculating agents. The sedimentation rate is also dependent on the separating factor of the decanter centrifuge, which is related to the centrifugal force.
The exterior bowl and the scroll conveyor rotate at different high speeds. This differential speed between the two is accountable for the sedimentation throughout the decanter centrifuge cylinder. A high differential speed results in a smaller residence time of the cake settlement, so it is necessary to keep the cake thickness to a minimum to avoid impairing the discharge quality.
Keeping the cake thickness to a minimum also aids in the improvement of the cake dewatering process. For this reason, it is necessary to obtain an optimal differential speed to balance the cake thickness and quality.
The characteristic above all affects the clarity of the liquid output which is dependent on the volumetric throughout rate, where a higher flow rate will result in a poor liquid clarity. Another characteristic that influences the clarity of the liquid output is the differential speed. A low differential speed results in a better clarity, therefore, aiding in the separation process. The G-Force also plays a role in the clarity of the liquid discharge. Higher G-force results in an increase in the separation of the solid particles from the liquid and yields a better clarity.
Oilfield Decanter Centrifuge Working Principle:
Decanter Centrifuge is driven by two motors. The main motor drives the drum and the outer casing of differential through belts while the auxiliary motor, after the differential shifting speed, drives the spiral propeller. This will make the drum and the spiral propeller rotate in the same direction with a certain differential speed.
Decanter Centrifuge Application:
Shenzhou LW Series Decanter Centrifuge is used to separate suspended solids ≥2μm in diameter and treat the drilling mud and fluids. It is especially effective when used in oilfield service industry, industrial service industry and especially in environmentally sensitive areas. This type of centrifuge is high in recovery rate, effective in solids control and remarkable in the reduction of cost spent on drilling mud resupplying and management. It is a very sophisticated dynamic balancing machine, able to operate stably with the whirling speed ranging from 0 to 3900 and generate centrifugal force of 3000G.
Shenzhou Decanter Centrifuge can meet with different requirements of mud treatment under various drilling conditions, that can do sedimentation and separation for particles more than 2 μm. After treatment, the mud can achieve ideal viscosity and proportion, resulting in better recycling, high efficiency, saving and environment protection.
The series of centrifuge by our company has been developed many years with the continuous improvement and optimization design, which possesses the characteristics of good result of separation and settlement, as well as large quantity, reliable work, longer life, lower energy consumption, easy maintenance, smooth operation, lower noises, etc.
To ensure that the effective treatment result and long service life, the important parts adopts high quality stainless steel, forging material, strengthen heat treatment and strict control processing. And on each part that easily wears take spraying wear-resisting layer and mosaic of hard alloy, etc. The overflow of the main drum mouth using adjustable poling board, it can be adjusted anytime according to different sludge treatment .
To meet the requirements of the development of modern drilling engineering, Shenzhou developed and equipped with the explosion-proof variable frequency control system which could adjust separation factor and drum rotational speed. By this new technology, make the centrifuge adapt property changing of mud during the operation process, that makes the treatment more effective and perfect.
A VFD ( Variable Frequency Drive ) module monitors and controls both the main and back electric drives. The operator can manage bowl and scroll speeds via a touchscreen that also displays input from the various sensors, including temperature, current, rotational speed and vibration.
A VFD ( Variable Frequency Drive ) module monitors and controls both the main and back electric drives. The operator can manage bowl and scroll speeds via a touchscreen that also displays input from the various sensors, including temperature, current, rotational speed and vibration.
Application Description of Decanter Centrifuge:
SHENZHOU decanter centrifuges of common models (as listed in the table of technical parameters) are applied to oil drilling solids control system and drilling waste management. In addition, SHENZHOU centrifuges of other models (including those in the following table) can also be widely used in the following industries:
Environmental Protection Industry
1. Thickening and dewatering of various sludge in municipal sewage treatment plants
2. City tap water sludge dewatering and city domestic sludge dewatering
3. Printing and dyeing wastewater separation
4. Paper-making wastewater separation
5.Desulfurization waste water in power plants
6. Ceramics wastewater separation
7. Tannery sludge dewatering
8. Mine stone wastewater
9. Coal-washing wastewater
10. Oil drilling mud separation
11. Textile wastewater
12. Electroplating wastewater
13. Integrated wastewater in pharmaceutical factories
Chemical Industry
1. PVC resin dewatering
2. ABS resin dewatering
3. Classified dewatering of non-metallic mine clay granularity
4. Fuel dewatering
5. Chemical fiber
6. Tar
Food Industry
1. Soy protein separation
2. Starch dewatering
3. Vegetable oil separation
4. Deslagging of fruit juice beverages
5. Peanut protein separation
6. Dewatering of distillers' grains
7. Cane sugar deslagging
8. Breeding industry
9. Butchery
10. Industrial wastewater in breweries
Pharmaceutical Industry
1. Separation of dregs extracted from traditional Chinese medicines
2. Saccharomycetes' corpse treatment
Other Industries
1. Recycling of paint powder
2. Separation of calcium sulfate in concrete admixtures
3. Recycling of plastics' crushed aggregates
4. Kaolin classification
5. Treatment of livestock' faeces
Models | Basket diameter (mm) | Rotation rate of basket (r/min) | Relative centrifugal force | Motor power(kw) | Productively M3/h | Weight(kg) | Dimension (L*W*H)mm |
LW250x900 | 250 | 5400 | 4000 | 11 | 1-5 | 1050 | 1800*1200*600 |
LW360x1200 | 360 | 1200 | 4200 | 15 | 3-12 | 2100 | 2600*1580*1040 |
LW360x1500 | 360 | 4200 | 3550 | 22 | 3-14 | 2600 | 2900*1600*1040 |
LW420x1750 | 420 | 4000 | 3750 | 37/45 | 6-30 | 3500 | 3120*1580*1070 |
LW420x2100 | 420 | 4000 | 3750 | 45 | 6-35 | 4100 | 3450*1580*1070 |
LW500x2000 | 500 | 3800 | 4000 | 45/55 | 10-40 | 6500 | 3600*2300*1400 |
LW500x2500 | 500 | 3800 | 4000 | 55/75 | 12-45 | 7200 | 4100*2300*1400 |
LW550x1900 | 550 | 3200 | 3154 | 45/55 | 13-50 | 4600 | 3400*1810*1110 |
LW550x2400 | 550 | 3200 | 3154 | 55/75 | 13-55 | 5600 | 3900*1810*1110 |
LW650x2000 | 650 | 2650 | 2500 | 55/75 | 15-65 | 7100 | 4000*2300*1400 |