Basic Info.
Trademark
ALONG BIOGAS
Origin
China
HS Code
8486909000
Production Capacity
100 Sets/Year
Product Description
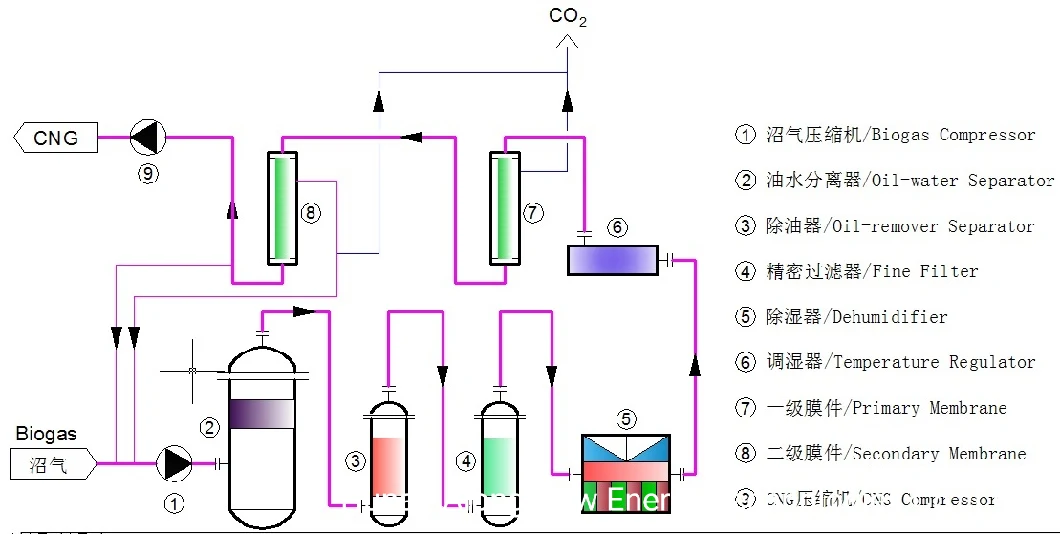
After two-stage desulphurization processes, then go through our GasDec system (Membrane Separation) for carbon removal, biogas could be upgraded to make CNG, for vehicle or going into national pipeline network.
The gas quality after upgrading as below:
Item | Quality Index | Comments | |
High thermal value | MJ/m3 | >31.4 | In the specific geographical area for vehicle driving, under the highest operation pressure, the water dew point shouldn't be higher than -13 degree.C; When lowest ambient temperature lower than -8 degree.C, the water dew point should be 5 degree.C lower than the lowest temperature. |
CO2 | % | ≤3.0 | |
Total Sulfur | mg/Nm3 | ≤200 | |
H2S | mg/Nm3 | ≤15 | |
O2 | % | ≤0.5 |
Procedures of our biogas upgrading system:
1, Primary Filter
The saturated water and partial particles in the raw digester gas are removed through the primary filter; 2, Boosting, Primary desulphurization
3, Fine desulphurization
The content of Hydrogen Sulfide is made lower than 50 mg/Nm3 through dry type desulphurization system; 4, Impurities Removal, Fine Cleaning System
The new dust and impurities in biogas could be removed through the Separator; Then delivered to Fine cleaning system for removals of water and tiny particles in order to protect membrane and guarantee its life-time;5. First MS (Membrane Separation)
The high quality compressed biogas goes into the first MS system through gas-distributing pipeline. The exhaust gas could be gathered or discharged into atmosphere;
6. Secondary MS (Membrane Separation)
The gas out of First-MS goes into Secondary MS system for final decarburization. The exhaust gas would totally return to the inlet of biogas compressor. Thiophane is added into the cleaned gas, after CNG compressor, through dispenser, to be delivered to gas station by tank lorry;
Main equipment list of our upgrading system:
1. Main non-standard equipment
Item | Equipment Name | Specifications | Qty | Comments |
1 | Primary Filter | 1Unit | ||
2 | Primary Cooler | 1Unit | ||
3 | Wet Desulphurization Tower | 1Unit | ||
4 | Secondary Filter | 1Unit | ||
5 | Dry Desulphurization Tower | 1Unit | ||
6 | Separator | 1Unit | ||
7 | Pregnant Groove | 1Unit | ||
8 | Regeneration Groove | 1Unit | ||
9 | Barren Liquor Groove | 1Unit | ||
10 | Sulfur Froth Groove | 1Unit | ||
11 | Underground Groove | 1Unit | ||
12 | Fine Cleaning System | 1 Set | ||
13 | First MS Assembly | 1 Batch | Imported | |
14 | Second MS Assembly | 1 Batch | Imported | |
15 | Buffer Tank | 1 Unit |
2. Main Operation Equipment List
Item | Equipment Name | Material | QTY | Comments |
1 | Biogas Blower | Case Iron | 2 Units | With back-up Anti-explosion |
2 | Desulphurization Pump | Case Iron +SS304 | 2 Units | With back-up Anti-explosion |
3 | Regeneration Pump | Case Iron +SS304 | 2 Units | With back-up Anti-explosion |
4 | Sulfur Froth Pump | Case Iron +SS304 | 2 Units | With back-up Anti-explosion |
5 | Supplement Pump | Case Iron +SS304 | 1 Unit | Anti-explosion |
6 | Biogas Compressor | Case Iron | 1 Unit | Anti-explosion, Variable frequency |
7 | CNG Compressor | Case Iron | 1 Unit | Anti-explosion, Variable frequency |
8 | Gas Dispenser | 1 Unit | Single line, Double nozzles & measuring | |
9 | Gas Odorization | 1 Unit |
3. Instruments & controlling
Item | Product Name | QTY | Comments |
1 | PLC Controlling Cabinet | 1 set | |
2 | PLC system | 1 set | |
3 | Operator Station | 2 units | |
4 | Complete On-line UPS | 1 unit | |
5 | Flow-meter | 2 units | |
6 | On-line analyzer | 2 units | |
7 | Pressure transmitter | 1 batch | |
8 | Pressure gauge | 1 batch | |
9 | Temperature gauge | 1 batch | |
10 | RTD | 1 batch | |
11 | Alertor | 1 batch | |
12 | Electrical control box | 1 batch |
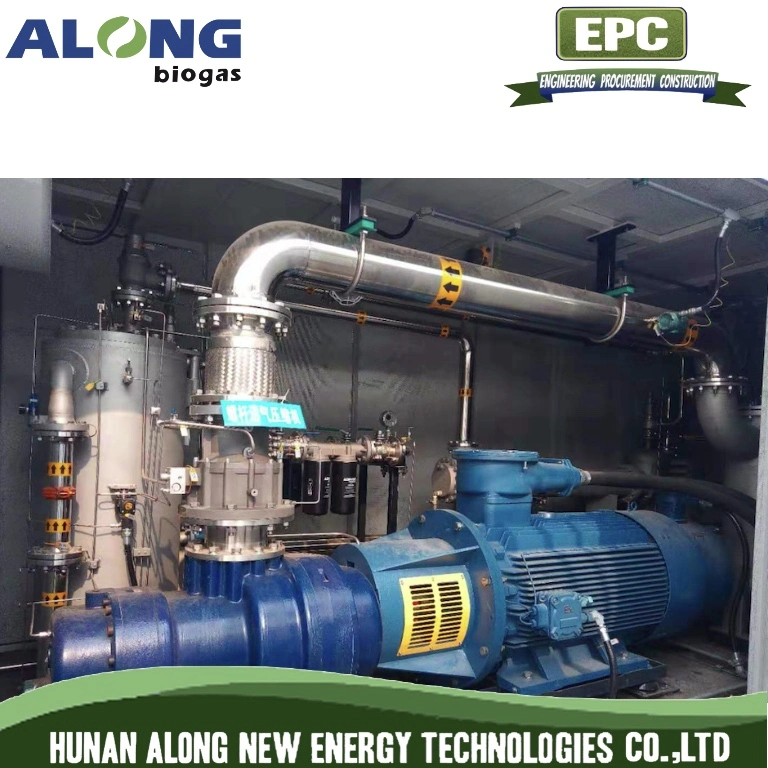
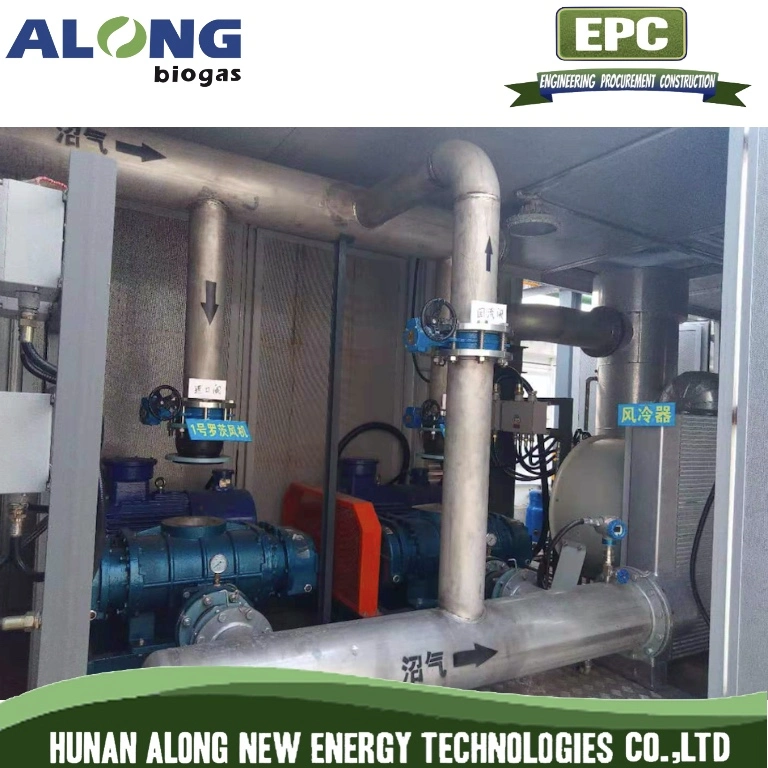
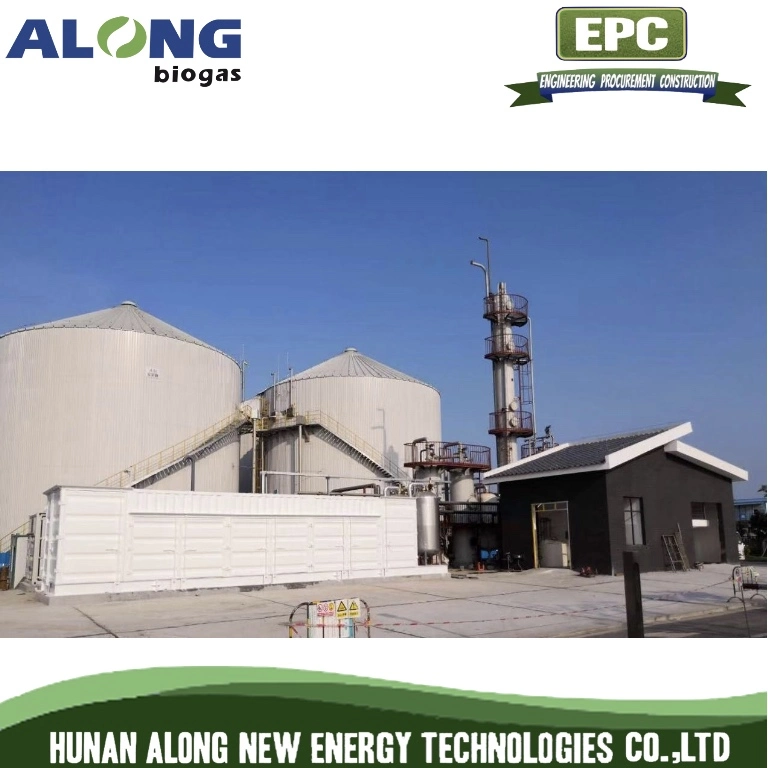
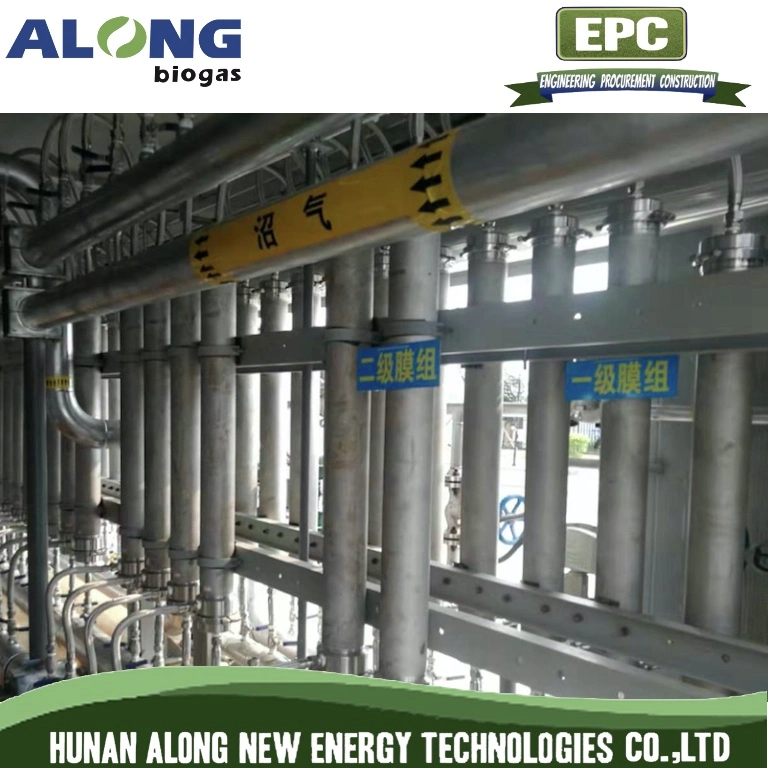