Basic Info.
Product Description
LNG STORAGE TANK
LNG Storage Tank, mainly used as static storage for LNG, adopts perlite or multilayer winding and high vacuum for thermal insulation. It could be designed in vertical or horizontal type with different volume. Our LNG storage tank could be designed and produced in accordance with ASME, EN, NB registration or Canadian registration number etc.
A liquefied natural gas storage tank or LNG storage tank is a specialized type of storage tank used for the storage of Liquefied Natural Gas. LNG storage tanks can be found in ground, above ground or in LNG carriers. The common characteristic of LNG Storage tanks is the ability to store LNG at the very low temperature of -162 °C (-260 °F).
As special equipment which has significant effects to public safety, LNG Storage Tank must have high requirement for quality and safety which we concern most. Large quantities of LNG storage tank have been exported to the United States, Canada and east Asian.
LNG storage tank | |||
Water Volume(M3) | Working Pressure(Bar) | Tare Weight(Kg) | Total Weight(Kg) |
63.8(Customized as users demands) | 11.21 | 24000 | 49500 |
239(Customized as users demands) | 5.1 | 94000 | 190700 |
In the shipping sector, liquefied natural gas (LNG) has firmly established itself as the fuel of choice for the future, according to a wide range of participants. Despite this upbeat outlook, one of the most significant barriers to switching to natural gas is the expensive initial investment required for LNG storage facilities. Supplier is continuing to investigate innovative ways of integrating technology in order to provide cost-effective storage solutions for gas-fueled boats of any size and LNG installed volume, regardless of their fuel source.
Shipping is a truly global business with fierce competition on an ongoing basis. Increased public pressure to reduce the sector's environmental effect only serves to increase customers' desire to lower their expenses. In order to save money and stay one step ahead of the competition, it may be necessary to implement innovative new solutions or repurpose existing technology from other industries. The latter method is often less complicated, involves less risks, and results in a shorter time to market. The evaluation of current technologies and their cost drivers, as a consequence, may aid in the creation of strategies for overcoming implementation roadblocks. Of course, each Supplier solution takes into account the unique needs of each customer, but this research outlines a few of the ways in which Supplier may help more customers in realizing the environmental and economic benefits of LNG.
Installations and equipment for liquefied natural gas - EN 1473
Cryogenic Liquid Vacuum Storage Tank
Euronorm It is the European standard EN 1473 Installation and equipment for liquefied natural gas, which serves as the overarching document for the design, building, and operation of all onshore LNG facilities. It includes installations for liquefaction and regasification, as well as storage facilities, which are often referred to as tanks in the industry. Environment compatibility, safety needs, risk assessments, and safety engineering are all addressed in detail in EN 1473, which specifies terminology and imposes standards to be taken into consideration throughout the design process. These LNG facilities are specified in detail in the standard and in Annex G: - LNG export terminal; - LNG receiving terminal; - LNG peak-shaving plants; and - LNG satellite plants.
Some parts of this standard have a direct impact on the design and construction of concrete tanks, while others have a less direct impact. This includes suggestions on how to evaluate safety and environmental compatibility, which are included in Chapter 4, for example. A thorough environmental impact assessment (EIA) must be carried out after the site has been determined. It is necessary to do this evaluation in order to determine the total amount of solids, liquids, and gases released by the facility during both regular operation and accidents. It is essential that plants be built in such a manner that gas is not constantly flared or vented, but is instead recovered to the greatest extent feasible, and that hazards to persons and property both within and outside the facility are minimized to a level that is widely considered acceptable. The study of the site may provide load scenarios that are important for the design, such as tsunamis or blast pressure waves,amongst other possibilities. It is necessary to include information on the existence of karst, gypsum and swelling clays in geological and tectonic soil surveys, as well as the susceptibility of the soil to liquefaction, the physical formation process, and the possibility for seismic activity in the future.
When constructing an LNG plant, it is necessary to do a risk assessment. The guidance in Annexes I, J, and K (which are given only for informational reasons) pertains to establishing frequency ranges, classes of consequence, degrees of risk, and acceptance criteria, among other things. A risk category is given to the plant based on a study of frequency ranges and consequence classes, and the plant is assigned to one of three risk categories. If the risk is acceptable, it must be lowered to a level that is as low as reasonably practicable (ALARP), if it is unacceptable, it falls into one of the categories listed above. In the annexes, the values specified are minimum requirements that may be increased by national laws or project specifications.
When doing a hazard and operation study (HAZOP), risk assessment is often included, but other methods are also allowed, such as failure mode and effect analysis (FMEA), event tree method (ETM), and fault tree method (FTM). It is necessary to categorize plant systems and components based on their relevance to safety within the scope of the risk assessment. Here, there is a division into two categories: class A, which includes systems that are critical to plant safety or protection systems that must be kept operational to ensure a minimum level of safety; and class B, which includes systems that perform functions that are critical to plant operation or systems whose failure could result in a major impact on the environment or create an additional hazard.
Sections 6.3 and 6.4 are particularly important for the design of concrete storage tanks, respectively. Section 6.3 and Annex H include specifics and illustrations of the different tank types, information that is complemented by the more comprehensive requirements of EN 14620 Part 1 (European Standard for Pressure Vessels). Because it covers spherical tanks as well as concrete tanks with both the main and secondary containers constructed of prestressed concrete, EN 1473 goes farther than EN 14620 in terms of the information that it provides. 6.4 defines design principles, which include criteria for fluid-tightness, maximum and minimum pressures, tank connections, thermal insulation, instrumentation, heating, and liquid level restrictions, among other things. These principles allow for the development of design criteria for the architecture of the facility, the minimum distance between tanks, and the consideration of potential sources of danger such as fire or blast pressure wave, among other things.
Construction of LNG Tanks - EN 14620 The European Standard EN 14620, which specifies the design and manufacture of site-built vertical, cylindrical, flat-bottomed steel tanks for the storage of refrigerated, liquefied gases with operating temperatures ranging from zero degrees Celsius to one hundred and sixty degrees Celsius, is divided into five parts:
- Part 1: Overarching Concepts
- Part 2: Components made of metal
- Part 3: Components made of concrete
- Part 4: Components of the insulation
- Part 5: Testing, drying, purging, and cooling-down procedures.
Part 1: Overarching Concepts
Part 1 establishes basic standards for the design and selection of tank types, as well as general performance parameters for the tanks in question. The process of conceptualizing and selecting tanks is described in full here. Temperatures ranging from 0 to 165 degrees Celsius and overpressures up to 500 millibars are within the area of application. When the pressure reaches 500 mbar, we refer to the vessel as a pressure vessel, which comes under the jurisdiction of EN 13445. This standard is limited to main containers built of steel exclusively, and it expressly excludes inner containers constructed of pre-tensioned concrete from its scope from a constructional standpoint. There are large quantities of methane, ethylene, and propylene stored in these tanks as well as large amounts of liquefied natural gas (LNG) and liquefied petroleum gas (LPG) stored in them. All of these gases are grouped together under the title "refrigerated liquefied gases" (RLGs). It is specified in EN 14620-1 what the physical characteristics of these gases are. The storage of argon (186 degrees Celsius), oxygen (183 degrees Celsius), and nitrogen (196 degrees Celsius) is not covered by EN 14620; these gases will be covered by EN 14620 Part 6, which is currently in preparation. With regard to the stored product, the capacity of the tank, and the design of the tank, the number of potential variants is vast, and the EN 14620 series' content cannot possibly cover every possibility or every detail. In the definition of the scope of the standard provided in Part 1, it is explicitly stated that if complete requirements for a specific design are not provided, it is the designer's responsibility to agree on the design principles and details, as well as the appropriate reliability, with the purchaser's authorized representative (or other representative). As a result, the configuration is defined as part of a front-end engineering design (FEED) for an LNG terminal, which is common procedure.
A specification for the LNG storage tanks for a given project is created, which specifies the rules, assumptions, analyses, and construction specifics for the tanks in question. LNG storage tanks are typically comprised of two containers: a steel inner container and a concrete exterior container, both of which are designed and constructed by separate specialized companies. It is not possible to carry out the design and, more precisely, the fabrication/construction in a separate manner. The duty for the steel, concrete, and insulation components, as well as overall responsibility for the coordination, are clearly delineated in Section 7 of this document. The specifics of the design and setup are covered in depth in the following sections.
Part 2: Components made of metal
BS EN 14620 Part 2 defines the basic criteria for metal components for tanks, including the materials to be used, the design and manufacture of the components, the welding techniques to be used, the welding, the construction and the installation of the components. The kinds of steel that are needed are determined by the type of liquefied gas that will be kept, as well as the temperature and type of tank that will be used. During normal operation and testing, the allowable stresses in plates and weld seams are specified, along with the minimum thickness of the metal shell, which is 40 mm for butane and propane tanks and 50 mm for ethylene, propane, and LNG tanks, respectively. The volume of liquid in the tank, along with seismic activity, causes the greatest amount of stress in the metal container. The minimum thickness for the metal plates has the effect of limiting the total capacity of the tank indirectly. Aside from design and calculations, fabrication and welding are all covered in detail in Section 2. Many components, depending on the diameter of the tank, have minimum plate thicknesses or cross-sectional dimensions that must be fulfilled before they may be used.
Part 3: Components made of concrete
According to the description in Part 1, the main (inner) container is constructed of steel, while Part 3 covers the principles and specifics for the design and construction of concrete components, i.e. the secondary or concrete outer container, as well as the concrete inner container. The requirements for the materials (concrete, conventional reinforcing, and prestressing steel) take up just one page of the specification. With regard to concrete, the user should refer to EN 1992-1-1 and EN 206, which are European standards. When using prestressed concrete components, the information provided in Annex A.1 only specifies the use of concrete class C40/50, a low water/cement ratio, and a suitable percentage of entrained air, and it permits the use of a reduced expansion coefficient and thermal material properties in the calculations. The pre-tensioning steel, anchorages, and ducts must all meet the requirements of EN 1992-1-1.
Also essential is the verification that the prestressing steel and anchorages are appropriate for the low temperatures to which they will be subjected throughout the construction process. Following the precedent set by the previous standard, BS 7777, the section on conventional steel reinforcement differentiates between temperatures above and below 20 degrees Celsius. Conventional reinforcement for design temperatures that do not dip below 20 degrees Celsius during regular operation or abnormal circumstances is only required to conform with EN 1992-1-1 during normal operation or abnormal conditions. Additional criteria must be met by the reinforcement and socket couplers in tension components that are exposed to temperatures below 20 degrees Celsius. In the case of a "liquid spill" load case, "cryogenic reinforcement," that is, reinforcement that contains a higher concentration of nickel and other alloying constituents, is typically used for the inside face of the concrete wall because the temperature at or near the level of the reinforcement can drop to approximately 150 degrees Celsius. Due to the fact that it is insulated against such temperatures by a so-called secondary bottom composed of 9 percent nickel steel and put inside the insulation, the foundation slab will not be impacted by this need.
It is possible to apply standard reinforcement on the outer face of a wall, even in winter, when temperatures may fall below 20 degrees Celsius. It should be noted that the temperature range of -40 to +100 degrees Celsius is specified in EN 1992-1-1, Annex C of the European Standard.
The tensile tests performed at low temperatures are described in full in Annex A.3. Annex B provides only extremely basic information on prestressed concrete tanks and does not define any specific criteria for their construction or use. For the connection between the wall and the base of the tank, the following theoretically conceivable couplings are illustrated: fixed (= monolithic), sliding, and pinned joints. Due to the boundary conditions imposed by subsoil, loads, and temperature in the case of LNG, it will be necessary to use monolithic connections in order to meet the requirements of the ultimate and serviceability limit state assessments.
Part 4: Components of the insulation
Details of the design requirements for and selection of insulating materials are provided in Part 4, as well as design of the vapor barrier to prevent the infiltration of water vapor from outside and the infiltration of the stored product's vapor from inside, as well as design and installation of the insulation system and commissioning and maintenance procedures. The boiling point of the liquefied gas kept in LNG tanks is lower than the temperature of the surrounding environment. The prevention of uncontrolled or excessive penetration of heat from evaporation is thus critical. Main purposes of insulation are to maintain a specified temperature below the boiling point, to protect the components of an exterior container that are not intended for such low temperatures, and to restrict the pace at which water boils off. Thermal insulation and foundation heating systems keep the soil from freezing and causing frost heave, as well as preventing the development of condensation and ice on the surfaces of the outer container's walls and floors. The appendix to Part 4 includes suggestions for the use of various insulating materials for individual tank components as well as for different kinds of tanks, as well as for individual tank components and tank types.
It is essential to note that in the case of LNG tanks, thermal insulation is not a minor component, but rather a critical component that must be considered in order to ensure the functioning and economics of the tank system are not compromised. As a result of this lack of clarity, the standard does not define a permitted value for the thermal insulation's quality, i.e. the maximum boil-off rate every 24 hours. The number that is often used is 0.05 percent of the tank's total capacity. For the purposes of this study, the boundary conditions include ambient temperature, solar radiation, and wind speed, all of which are specified in the tank's design.
Part 5: Testing, drying, purging, and cooling-down procedures.
Testing, drying, purging, and cooling of tanks are all covered in detail in Part 5 of this specification. Tank tests are split into two categories: hydrostatic and pneumatic. In the case of single-wall tanks, these two tests are carried out in conjunction with one another. The testing pressure is applied in the vapor area above the water, above the surface of the water. In the case of double-wall and complete containment tanks, the two tests may be carried out either simultaneously or independently from one another. The pressure test entails providing a pressure that is 1.25 times the design pressure throughout the testing period. Pressure-relief valves must be inserted and adjusted to the desired pressure before the test can begin; they must be withdrawn once the test is completed. Partially vacuumed tanks are also checked to ensure that they operate at the design negative pressure of the tank, which is often 5 or 10 mbarg. A partial vacuum may be created by using a pump or by simply decreasing the level of the water in the tank. A distinction is made in the liquid-tightness test between the hydrostatic pressure at full height (FH) and the hydrostatic pressure at half height (PH). It is filled to its maximum design level in the former, while it is filled to its maximum design level in the latter. In the latter case, the filling level is calculated as the product of 1.25 times the maximum design liquid level and the density of the corresponding liquid gas in the relevant liquid gas.
On the one hand, the combination of filling with water and internal pressure increases the strain on the base slab and foundation; on the other hand, a tank filled with water decreases the volume to which internal pressure may be applied by a significant amount. As an added bonus, it shortens the duration. The choice on which technique to choose is heavily influenced by the circumstances in the area.
API 620 - the American Standard for Steel Tanks
A specification for the design and construction of large, welded, site-built steel tanks for holding petroleum intermediates (gases or vapors), completed products, and other liquid goods needed by different sectors of industry is defined by the American Petroleum Institute (API 620). The standard applies to tanks with a single vertical axis of rotation, metal temperatures that do not exceed 120 degrees Celsius, and overpressures of one bar or less. For tanks designed for storing both liquids and gases or vapors above the surface of the liquid, as well as for tanks meant only for storing gases and vapors, the requirements of the standard are applicable.
API 620 contains two essential appendices: Appendix Q and Appendix R. Both of these appendices are required reading. It is intended that the requirements in these appendices serve as a guide for the selection of tank materials, and for the design and construction of tanks for the storage of liquefied gases in general. It is possible to build a tank for liquefied gases with a single or double wall construction, with the latter consisting of an inner container for holding the liquid and an outside container for protecting the insulation and accommodating low gas pressure. In a double-wall tank, a two-part construction in which the outer container is not intended to accept the product in the inner container, the product is contained inside the outer container. Materials, design, and testing of the inner and outer containers of a double-wall tank are thus subject to varying regulations depending on their location inside the tank.
Appendix R specifies the requirements for designing tanks for the storage of products at temperatures as low as 50 degrees Celsius, whereas Appendix Q specifies the requirements for designing tanks for the storage of liquefied ethane, ethylene, and methane at temperatures as low as 165 degrees Celsius, with an internal pressure of no more than 1 bar in each of these cases. This standard is still used for the design and construction of a large number of inner containers for LNG tanks.
API 625 - Using Concrete and Steel in the Same Project
API 625 was published in its first version in August 2010 and, along with API 620, appendices Q and R, and ACI 376, formed a comprehensive American code. API 625 is the equivalent to EN 14620 in the United States. It establishes the roles and duties of buyers and suppliers, as well as the areas in which both parties must come to terms. Also included are suggestions for selecting a storage concept on the basis of a risk assessment, examples of single, double, and complete containment tank systems, and a breakdown of the various criteria for each kind of storage system. A number of possible configurations of the three distinct kinds of tank system are shown, and in terms of information, they do not vary from the definitions provided in BS 7777 or EN 14620-1, respectively.
A chapter on design and performance requirements is included in API 625, as well as sections on insulation, hydrotests, pressure testing, purging, and cooling-down procedures. In this way, it covers the material of EN 14620 parts 1, 4, and 5 in its entirety. API 620 is used for the selection of materials, the design and calculations, the manufacturing, the building, the inspections, and the testing of metal containers. The appendix to be used, either Q or R, is determined by the temperature range and design temperature of the metal in question. The American Concrete Institute 376 standard is used for the selection of materials, the design and calculations, the fabrication, the building, and the testing of concrete tanks.
ACI 376 - American Concrete Institute Steel Tank
ACI 376 specifies the requirements for the design and construction of reinforced and prestressed concrete structures for the storage and retention of refrigerated and liquefied gases with operating temperatures ranging from -4 to 200 degrees Celsius, as well as for the storage and retention of liquefied gases. As a result, it also has oxygen and nitrogen storage tanks. Furthermore, it allows for the application of the regulations contained within it to the concrete foundations of double-wall steel tanks as well. The configuration of the tank wall, base slab, roof, and foundation are all included in the constructional specifications. The standard also governs a wide range of other issues, from the scope of the soil survey to the standards for construction to the procedures for commissioning and decommissioning. Tanks made of reinforced and prestressed concrete may be used for two main purposes: storage and transportation.
- The most commonly seen use for these containers is as secondary containers. The reason for this is that they protect the stored product from activities from the outside while also protecting the surrounding environment from mishaps that occur within the tank. Concrete tanks are also permitted to be used as main containers under the rules. ACI 376 defines the minimum requirements for concrete inner containers and provides specifics in section 6.2, while all other rules are extremely broad when it comes to concrete inner containers.
Both the definition of the scope of the standard and the substance of the standard do not make any suggestions about membrane tanks in this regard. When using a membrane tank, the inner container is comprised of a thin metal layer (membrane) that is not self-supporting and is supported by the concrete outer container via the use of insulation. In the spring of 2015, work started on a modification of the standard that would incorporate membrane tanks. It is feasible to use the criteria to build concrete tanks as main and secondary containers with extra considerations and calculations, as well as taking into account the hydrostatic pressure on the concrete wall as an operational condition. In addition, ACI 376 does not include any information on steel primary or secondary containers, which must be built in accordance with API 620.
Types of LNG Storage Tanks
Type of LNG tanks
Liquefied gas storage tanks are classified according to their kind and size according to a variety of standards and rules that vary in terms of when they were issued as well as the amount of information they provide. The two German standards, DIN EN 1473 and DIN EN 14620, are even diametrically opposed in terms of the language they use. This section will make use of either the terminology found in the British counterpart, BS EN 1473, or the terms found in API 625. BS EN 1473 is the British equivalent of API 625. From a practical standpoint, the term "containment tank system," as used in API 625, seems to be the most suitable, since the many, but coordinated, components work together to form a cohesive system as a result of their interaction. According to the standards EEMUA, BS 7777, EN 1473, EN 14620-1, NFPA 59A, and API 625, containment tank systems may be classified as single, double, or complete containment tank systems. There is one additional tank type that is described in more depth in the European standards EN 1473 and EN 14620, and that is the membrane tank.
Until the 1970s, the only kind of tank that was constructed was the single-wall tank. It was the hazard scenarios resulting from abnormal actions such as failure of the inner tank, fire, blast pressure wave, and impact that inspired the subsequent further development of the various types of tanks or tank systems, and the associated requirements placed on the materials and construction details. Because of the dangers that a tank failure poses to the surrounding regions, it is essential to choose the appropriate kind of tank system.
It will be shown, using the failure of the inner container, the consequences of such a failure on the tank as a whole and its surroundings for three widely used tank systems. It will also be discussed how these three tank systems have evolved over time.
- System with a single containment tank
In the region (impounding basin) surrounded by the bund wall, the liquefied gas seeps out via the cracks. As specified in EN 14620-1, the distance between the main container and the bund wall may be as much as 20 meters. Thus, an expansive region enclosed by an earthen wall that is partially filled with LNG results. The evaporation of the LNG and the following pool fire (which is very probable) will have a significant impact on a huge portion of the plant. No safeguards can be put in place to keep the heat radiation from harming surrounding buildings and structures, as well as other components of the plant.
Double containment tank system
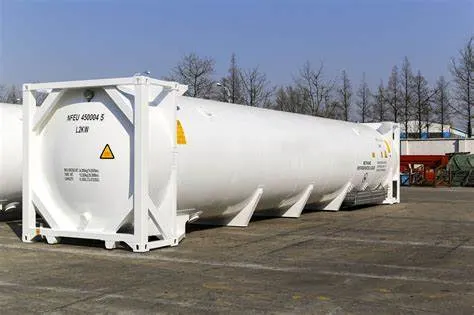
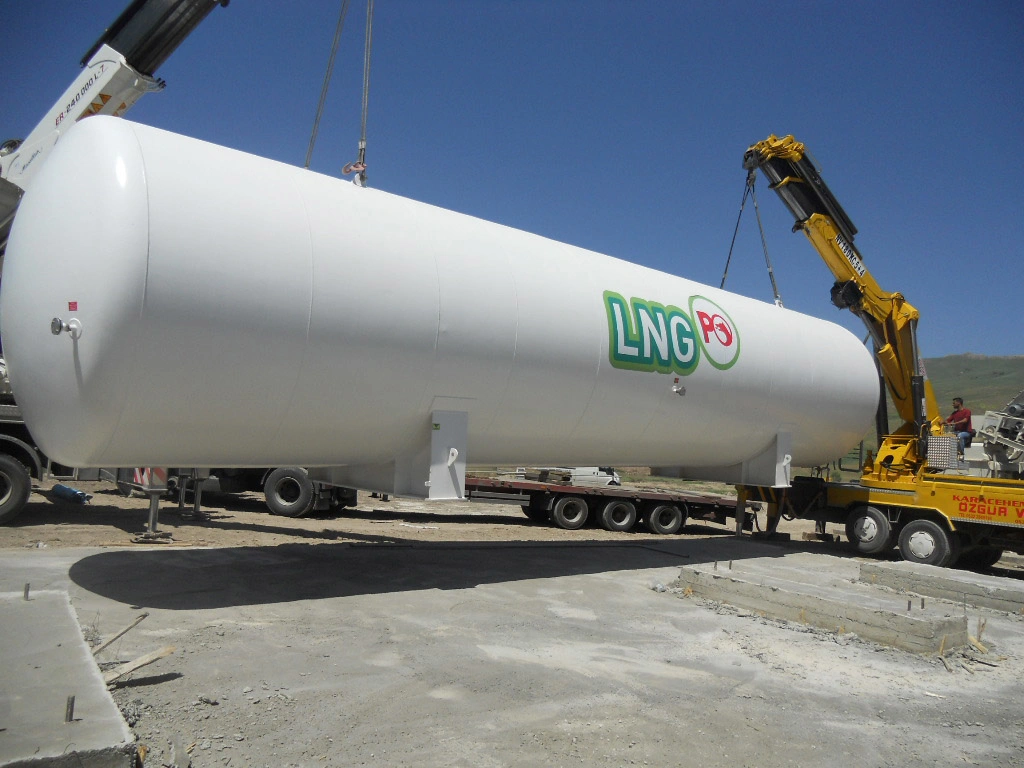
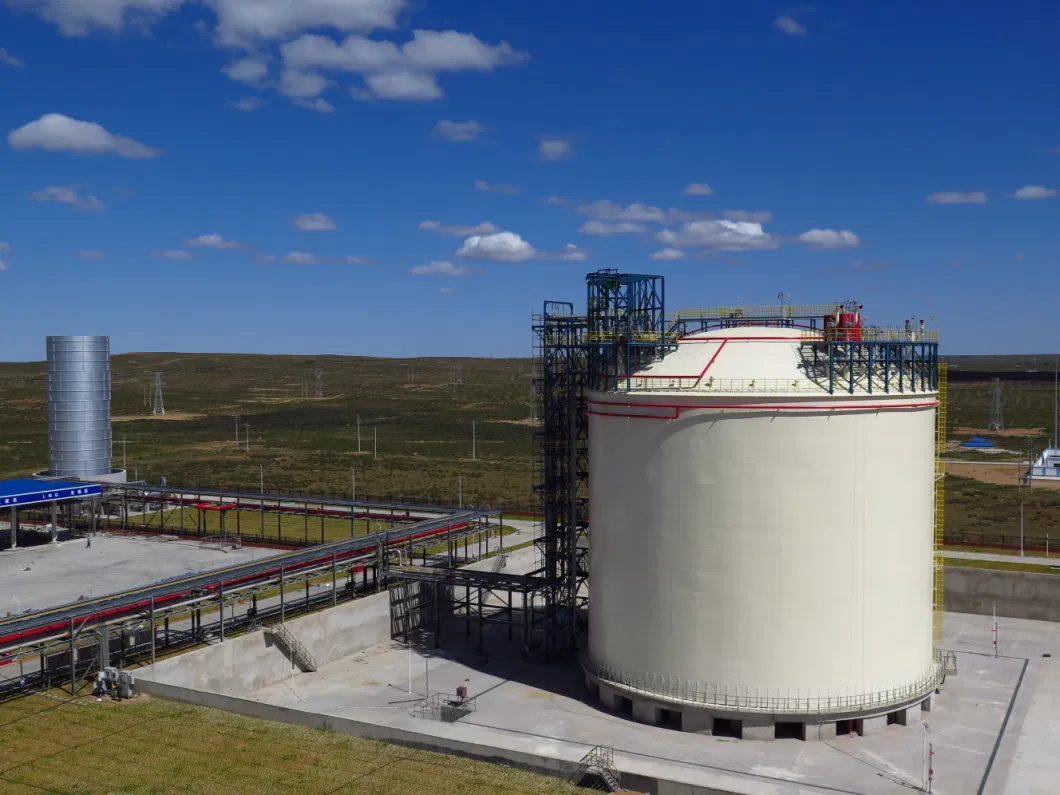