- Overview
- About Us
- Product Description
- Process Technology
- Customer Benefits
- Reference List
Basic Info.
Product Description
Greenfir is a professional natural gas processing & liquefaction plant, air separation unit, heat exchanger, reciprocating piston compressor, cryogenic cold box, fractionating column manufacturer and solutions provider with ISO 9001: 2015, ISO 14001: 2015, ISO 45001: 2018 and ASME U certified.
We offer skid-mounted solutions optimized for each specific project, covering the following applications: Air Separation Plant, LNG Plant, Gas Purification & Liquefaction Unit, CNG/ LNG/ L-CNG Filling Station, Flare Gas Recovery Unit and Hydrogen Purification Unit, etc. We can deliver skid-mounted solutions customized to meet client's challenges and requirements (including adverse weather conditions, transportation and plot area limitations, etc).
We treat all the cryogenic solutions with serious attitudes and professional experience. Combined with our knowledge and experience, Greenfir provides each client with a technology-leading solution you can count on and bring a wider range of options and more profits.
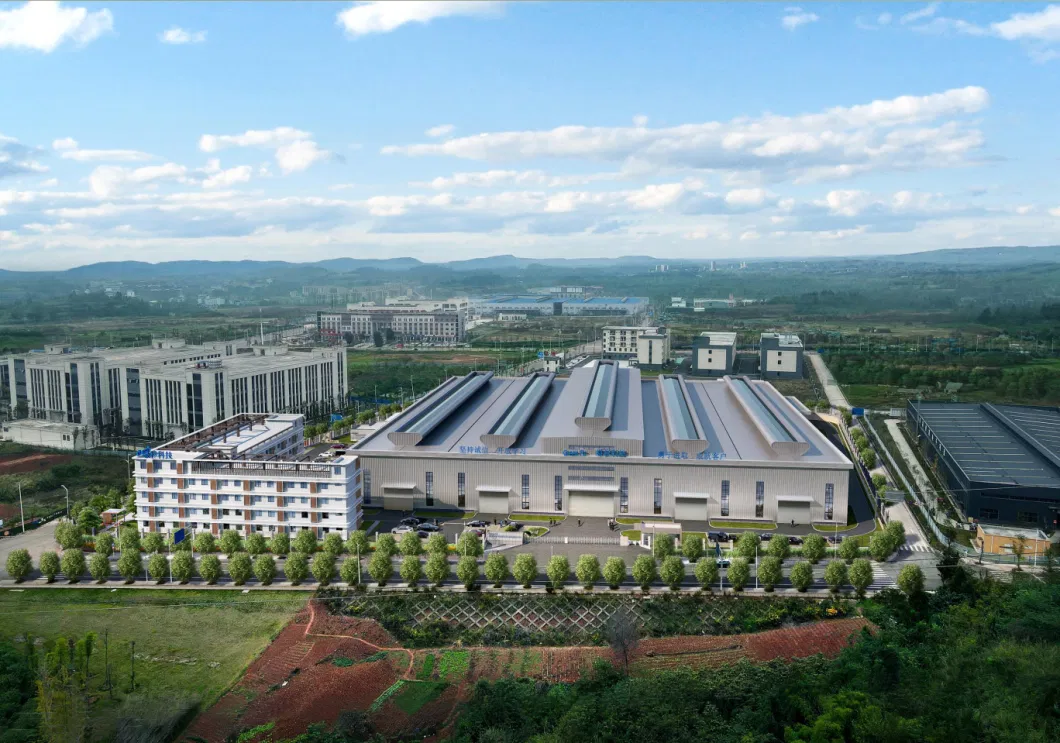
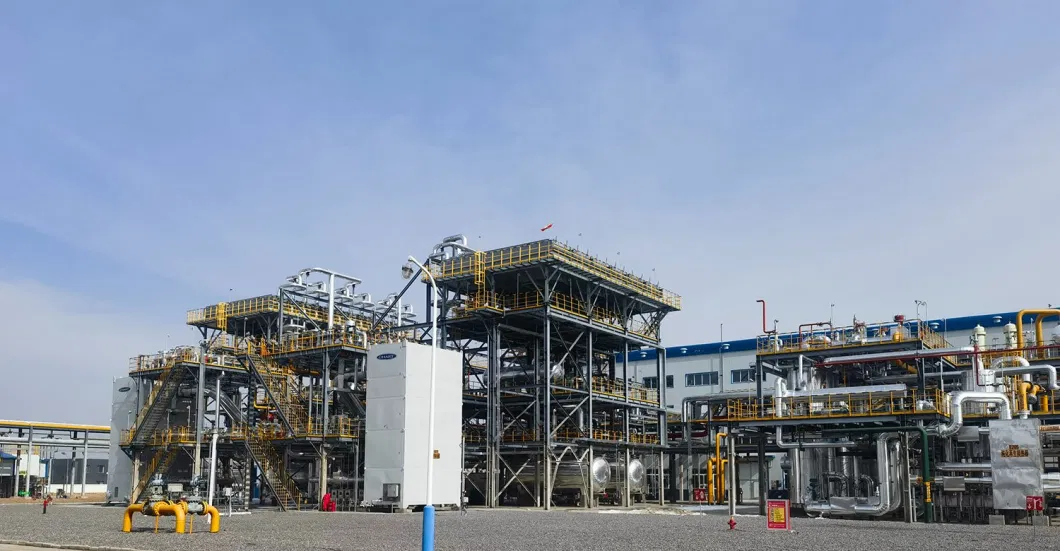
Greenfir provides solutions for your gas processing project, including shop fabrication, construction management, startup, and operations. We offer a range of solutions to best meet your gas processing needs - from straightforward dew pointing operations, to maximum NGL recovery.
Modular Design for Reduced Costs and Predictable Timelines
Our modular gas processing plants are factory-built using a unique design and construction approach that allows for quick fabrication and superior quality control. Due to pre-fabricated construction, your plant can be shipped by truck - even to remote locations. Upon delivery to a prepared worksite, the equipment is ready to install. Modules are designed to fit together rapidly, significantly reducing site construction time, expense and associated delays.
Greenfir liquefaction technologies are mostly based on the MR (mixed refrigerant) technology. It is designed with a closed loop refrigerant cycle, thereby eliminating make-up or chemical/ logistics handling for the refrigerant. The main elements of the plant are as listed below, while different modules can be incorporated to improve the efficiency of the plant according to the specific project requirements.
Main System- Filtering & Metering Skid
- Gas Purification System (Acid Gas Removal package, Dehydration Package, and Mercury Removal Package)
- Liquefaction (Cold Box, MR Compressor, etc.)
- LNG Storage
- LNG Loading System
- Utilities (Instrument Air & PSA Nitrogen Generattion Package, Demineralized Water System, Hot Transfer Oil System)
- Instrumentation Control System
- Electrical Control System
- Feed Gas Booster Compressor(s) (Optional)
- Nitrogen Removal Column (Optional)
- Heavy Hydrocarbons Separation (Optional)
- Biol-off Gas Handling (BOG Compressor) (Optional)
- Power Generation (Optional)
- etc.
- Robust and reliable technology that is simple to operate.
- Designed for unmanned operation.
- Easy start-up and shut down of all systems.
- Quick and easy capacity control.
- Compact and modularized design ensures easy shipment and cheaper installation.
- The lowest specific power consumption in small size plants.
- All components based on conventional parts and proven technology -> Spares can be delivered quickly.
- Reliable main rotating machinery with high efficiency.
- Local control of LNG export -> truck driver handles the loading.
- Fast project delivery time (FOB 7 months for the MRC Process).
- Broad range of applications, biogas, pipeline, CBM and associated gas
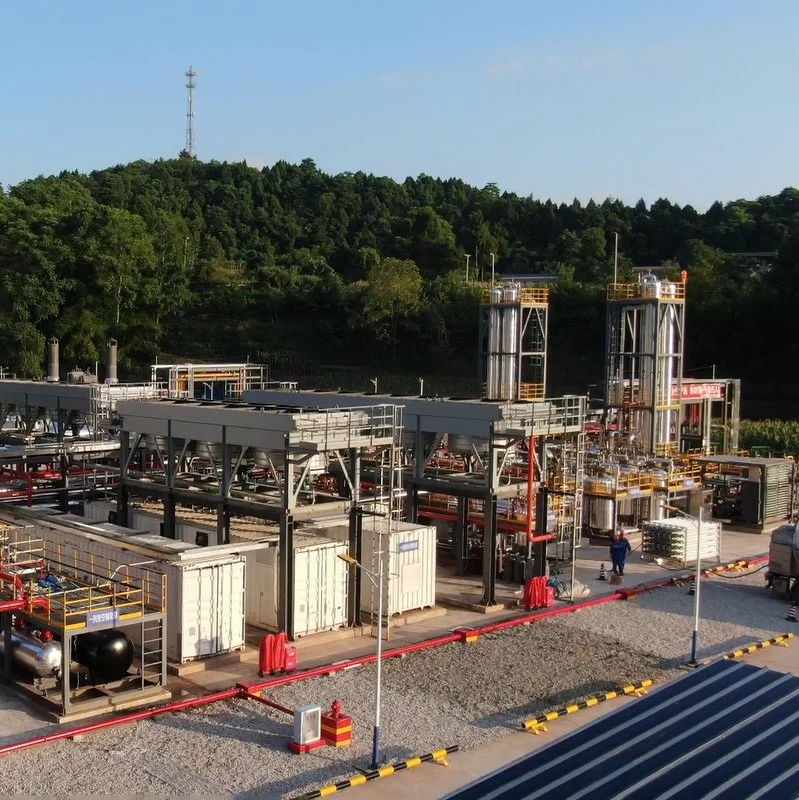
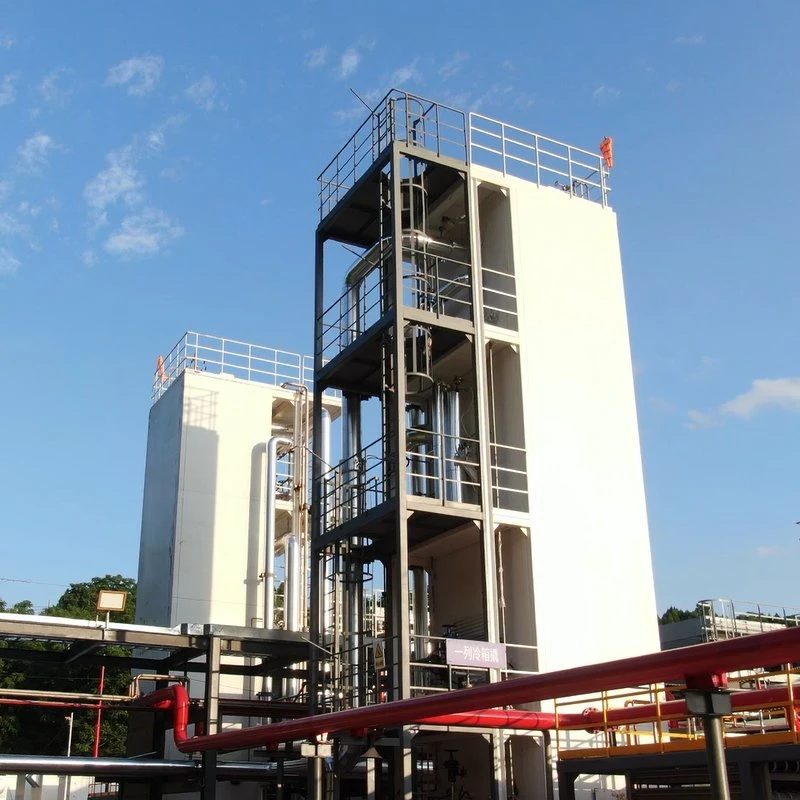
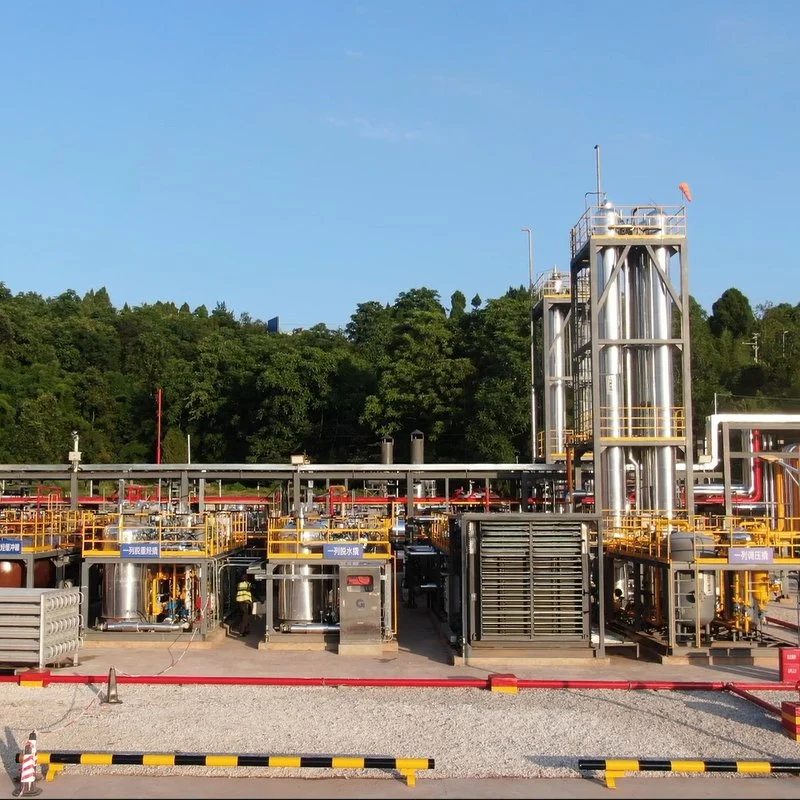
Our extensive service offerings, coupled with our unmatched technical knowledge and experience, can help you focus on profitability.
The first step in natural gas processing is to separate the raw natural gas from the water and condensate. Second, the contaminants, which include hydrogen sulphide (H2S), carbon dioxide (CO2), mercaptans, carbonyl sulphide (COS) and mercury, must be removed.
Project | Scope of Supply | Capacity | Quantity | Location | Year | |
Natural Gas Purification, Liquefaction Plant | ||||||
50,000 Nm3/day Wellhead Gas Recovery Project | EPC | 1 | China | Nov. 2016 | ||
30,000 Nm3/day Mini LNG Plant | EPC | 2 | China | May, 2017 | ||
30,000 Nm3/day Wellhead Gas Recovery Project | EPC | 1 | China | May, 2017 | ||
30,000 Nm3/day Mini LNG Plant | EPC | 1 | China | Nov. 2018 | ||
50,000 Nm3/day Wellhead Gas Recovery Project | EPC | 1 | China | Nov. 2019 | ||
60,000 Nm3/day Mini LNG Plant | EPC | 1 | China | Nov. 2018 | ||
Demethanizer and Deethanizer Rectification System | EP | 20,000 Nm3/day | Kazakhstan | Jul. 2020 | ||
CNPC 100,000 Nm3/h Mini LNG Plant | EPC | 2 | China | Jan. 2021 | ||
ARV 50 TPD Mini LNG Plant Project | EP, Supervision Commissioning & Start-up | 50 TPD | 1 | Irian | Apr. 2021 | |
MAN 3.5 MMSCFD Mini LNG Plant Project | EP, Supervision Commissioning & Start-up | 3.5 MMSCFD | 1 | Irian | Apr. 2021 | |
50,000 Nm3/day Mini LNG Plant | EPC | 1 | China | Aug. 2021 | ||
Ethylene Compressor Station | EP, Supervision Commissioning & Start-up | 17.88 MMSCFD | Irian | Apr. 2022 | ||
MAR 20 MMSCFD Amine Sweetening Package Project | EP, Supervision Commissioning & Start-up | 20 MMSCFD | 1 | Irian | Dec. 2022 | |
KHE 13 MMSCFD Field Flare Gas Recovery Project | EP, Supervision Commissioning & Start-up | 13 MMSCFD | 1 | Irian | Dec. 2022 | |
100,000 Nm3/h Mini LNG Plant | EPC | 2 | China | Dec 2022 | ||
Deethanizer Rectification System | EP | 30,000 Nm3/day | 1 | Kazakhstan | Mar. 2023 |